Pultrusion
... providing long lasting & new age “GREEN” solution to ageing Infrastructure.
The pultrusion process starts with racks or creels holding rolls of fiber mat or doffs of fiber roving. Most often the reinforcement is fiberglass, but it can be carbon, aramid, or a mixture. This raw fiber is pulled off the racks and guided through a resin bath or resin impregnation system. Resin can also be injected directly into the die in some pultrusion systems.
The raw resin is almost always a thermosetting resin, and is sometimes combined with fillers, catalysts, and pigments. The fiber reinforcement becomes fully impregnated (wetted-out) with the resin such that all the fiber filaments are thoroughly saturated with the resin mixture.
As the resin rich fiber exits the resin impregnation system, the un-cured composite material is guided through a series of tooling. This custom tooling helps arrange and organize the fiber into the correct shape, while excess resin is squeezed out, also known as “debulking.” This tooling is known as a “pre-former.” Often continuous strand mat and surface veils are added in this step to increase structure and surface finish.
Once the resin impregnated fiber is organized and removed of excess resin, the composite will pass through a heated steel die. Precisely machined and often chromed, the die is heated to a constant temperature, and may have several zones of temperature through-out its length, which will cure the thermosetting resin. The profile that exits the die is now a cured pultruded Fiber Reinforced Polymer (FRP) composite.
This FRP profile is pinched and pulled by a “gripper” system. Either caterpillar tracks or hydraulic clamps are used to pull the composite through the pultrusion die on a continuous basis. At the end of this pultrusion machine is a cut-off saw. The pultruded profiles are cut to the specific length and stacked for delivery.
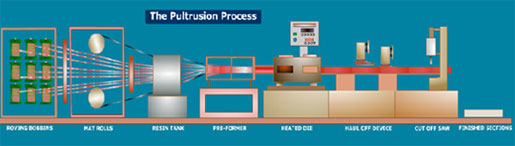